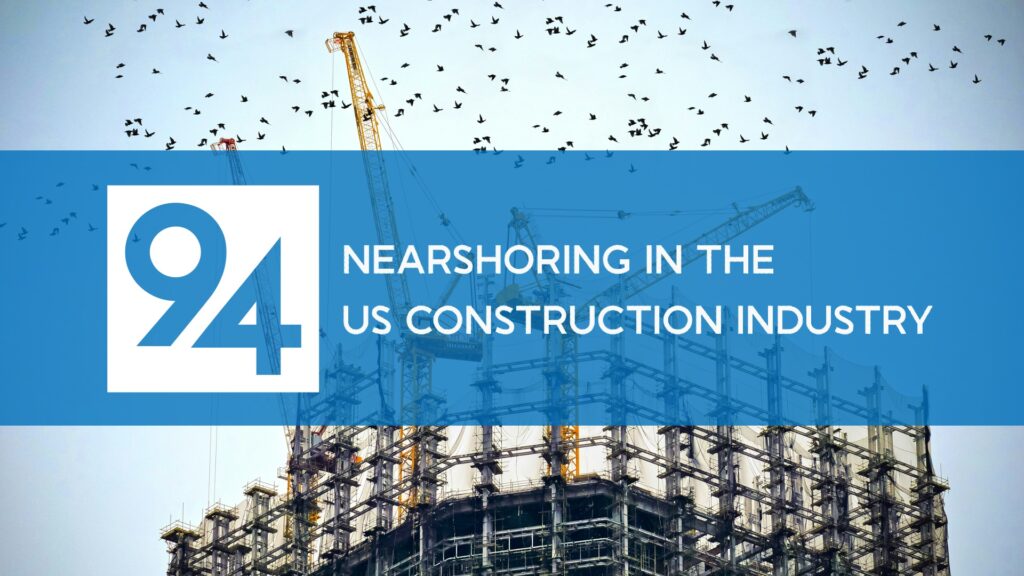
Triggered by the trade wars between China and the US in 2018 and supported by the USMCA—which eliminates trade tariffs on most goods between the US, Mexico, and Canada—there’s been a major shift in the origin of manufactured goods. This shift has been further accelerated by the COVID-19 pandemic’s supply chain disruptions and global geopolitical instability. These factors have collectively prompted businesses to reevaluate and often relocate their manufacturing bases closer to home, enhancing the appeal of nearshoring options in North America.
At the heart of the reshuffling of global trade relationships is China, once considered “the manufacturer of the world,” and has since moved upstream to higher-value manufacturing and technology development. With an economy second only to the US in terms of GDP, China has entered more direct competition with the US, resulting in a decoupling of their economies.
While Canada has benefited from nearshoring, Mexico’s cheap labor has been better suited to absorb the production of former Chinese-manufactured goods. As a result, Mexico has seen major economic benefits such as a boom in manufacturing exports, increased earnings for the lower classes employed in these industries, and a strengthening of the peso against the dollar. According to Deloitte Insights, while tariffs play an important role in prompting American businesses to move manufacturing to Mexico, other major factors include shorter lead times, competitive labor costs, a qualified workforce, favorable tax structures, and defendable intellectual property rights.[1]
The construction industry has also been impacted, and at Nine Four Ventures, we’re witnessing it firsthand through our portfolio company Latii. Starting with the windows and doors industry, Latii is pairing Latin American manufacturing with American developers through an AI-enabled streamlined marketplace platform. Building on our experience with Latii, we are keen to dissect the impact of the nearshoring trend to understand which sub-industries have been most affected and where opportunities for company formation lie. To this end, we have used the United Nations Comtrade Database to analyze key construction-related goods, ranging from concrete to HVAC systems.[2] While this is not an exhaustive analysis, we believe it provides sufficient insight to identify potential opportunities. The complete list of categories considered and their HS codes can be found at the end of this post.
US Construction-Related Imports
Notwithstanding the decoupling from China, our basket of US construction-related imports has grown at an impressive 7.3% CAGR, significantly outpacing the overall growth of the US construction industry.
Breaking down our basket of construction-related imports, we find several categories that account for an outsized slice of the pie. Leading these categories are electrical panels, ventilation components, structural steel, electrical wires and cables, and electrical switches and sockets.
Decoupling from China
Returning to our focus on the US-Mexico-China trade dynamics, Mexico was already the primary trade partner of the US before the trade war. Together, China and Mexico accounted for almost 60% of this market at its peak in 2018. Since then, China’s share of construction-related imports has dropped from 25% to 11%. Although Mexico has gained the most in this transition, its increase of 4% in market share pales in comparison to China’s losses. Other countries are also stepping in to fill the gap in the supply chain shuffle, such as Thailand growing from 2% to 5%; India from 1% to 3%; Vietnam from 1% to 3%; and Korea from 3% to 4%.
To identify areas of opportunity, we further dissected the data to understand where China’s trade gap is most pronounced, and compared this to the total imports for the same categories in the US. We focused this analysis on the period from 2018 to 2023, specifically examining the time after the initiation of the trade war.
The first thing that became evident is that the nearshoring alternative has proven viable almost universally. Except for three categories, all others have seen growth in total US imports, indicating that other countries were able to take over Chinese manufacturing supply.
Takeaway
In conclusion, the nearshoring effect has been effective in moving construction-related supply chains from China to other countries, with Mexico being the primary beneficiary. The proof is the continuous growth of total imports in the past five years, while imports led by China dropped by 36.7% during the same period.
Zooming in, opportunities may exist in the few categories that have declined in total U.S. imports, where increased production could help meet the demand. For instance, the decline in U.S. imports of roofing materials, HVAC systems, and flooring materials presents a unique opportunity for traditional operating businesses to step in. However, further analysis at the category level is important, because the underlying cause for the gap could be due to a decrease in market size, or an increase in local production.
Regardless, the shift in supply chains and emerging challenges set the stage for startups like Latii to focus on innovative solutions to connect supply and demand across the border more efficiently and reliably.
HS Codes
Written by: MBA Associate Intern, JP Villafuerte
The information provided in this blog is not intended to be financial advice or solicitation for any purchase or sale of securities and is the opinion of the author at the time of publication. Investing in securities entails risk, including the risk of principal. Some of the information presented has been provided by third parties, has not been independently verified, and is subject to change without notice. The opinions stated are the opinions of Nine Four Ventures at the time of publication. Past performance is not a guarantee of future returns.
[1] https://www2.deloitte.com/us/en/insights/economy/issues-by-the-numbers/advantages-of-nearshoring-mexico.html